Brown Tungsten Oxide SEM Micrograph
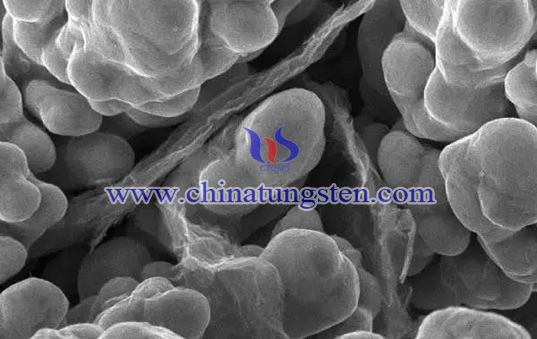
SEM Operating Principle
Scanning electron microscope manufacture is based on the interaction of electrons with matter. SEM is the use of very fine focus high-energy electron beam on the specimen scanning, inspired a variety of physical information. By accepting this information, the enlarged and displayed image, to obtain a test sample surface morphology.
Physical phenomena of electron beam acted on the surfacce of sample.
When high-energy incident on the sample surface scanning electron bombardment bunch of fine, regional excited to generate secondary electrons, Auger electrons, characteristic x-ray and X-ray continuous spectrum, backscattered electrons, transmission electron, as well as in the visible, ultraviolet , infrared region of the electromagnetic radiation generated. At the same time it can produce electron - hole pairs lattice vibrations (phonons), electronic oscillations (plasma).
SEM Portfolio analysis function
The present SEM Portfolio analysis functions are: 1)X-ray microanalysis system, which is mainly used for qualitative and quantitative analysis of elements, and analysis of chemical information composition of the sample;(2)Electron backscatter system, which is mainly used to study crystal and minerals.(3)Microscopic hot stage and cooling stage system which is mainly used to observe the micro structure change of materials during heating and colding. (4)Pull system, which is mainly used to observe and analyze micro structure changes of material during pulling.
Brown tungsten oxide appearance
Observing by SEM, we can verify that brown tungsten oxide is prepared by ammonium paratungstate, by thermal decomposition from blue tungsten oxide and violet tungsten oxide. Almost every WO2.72 turns into flat and smooth grains. Besides, we can observe that its general producing method is calcinating APT under 500 degree celsius into tungsten trioxide, or reducted into blue tungsten oxide under 450 degree celsius.
Tungsten oxide product is reducted by hydrogen into tungsten powder. The reduction process can be devided into two steps: Firstly reduced under 630 degree celsius into tungsten dioxide; Then reduced into tungsten powder under 820 degree celsius. It will let kalium make its full use to control the particle size of tungsten powder. The tungsten powder can be pressed into rectangular bar. Charge the bar in the hydrogen and heat it with resistance( the temperature is around 3000 degree celsius.) The density of tungsten bar can reach 85%. This kind of tungsten bar can be processed into 3mm tungsten rod, then processed into tungsten filament of different dimensions.